ISO 9001 & IATF 16949 certified as developer & producer of electromagnets.
Hydrogen
Discover how our innovative electromagnet solutions and advanced technologies are shaping the hydrogen technology of tomorrow.
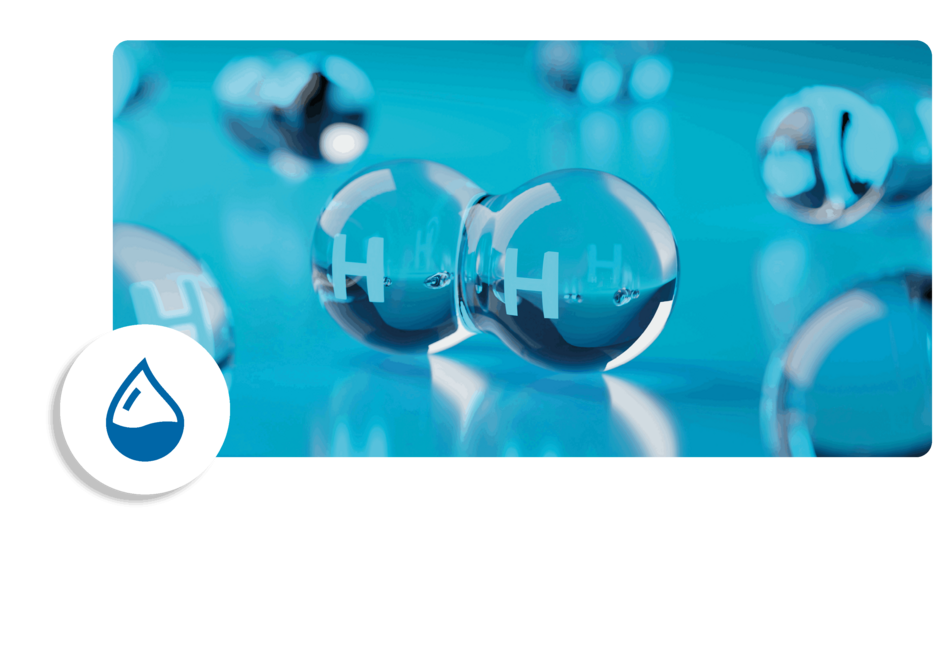
Use of electromagnets
Efficiency and precision: electromagnets optimise hydrogen technology
Electromagnets are essential components in hydrogen technology. They are used in critical applications such as the precise control of valves, pressure regulation in compressors or the handling of storage and conveying systems.
Application examples for electromagnets in the hydrogen sector
- Proportional solenoid for high-pressure control unit
- Switching solenoid for tank valves or drain valves
- And many more
Precision and reliability in demanding applications
Their ability to generate high forces in the smallest of spaces, coupled with fast and precise switching performance, makes our electromagnets ideal for demanding tasks in hydrogen systems. Whether for fuel cells, hydrogen-powered combustion engines or hydrogen infrastructure, our electromagnetic systems guarantee robustness and durability.
Technical solutions are available for extreme conditions such as high pressures, temperatures, aggressive media or corrosive environments, thus ensuring the reliable functioning of the overall system. Our electromagnets thus make a decisive contribution to the efficiency and safety of modern hydrogen systems.
Your advantages with Schramme
Development and production of electromagnets in hydrogen technology
Magnetbau Schramme is your experienced partner for the development and series production of high-quality electromagnets for hydrogen technology. With decades of expertise, we offer customised solutions that meet the highest standards of precision, efficiency and reliability and can be seamlessly integrated into demanding hydrogen applications.
From the initial concept phase to series production, we provide you with comprehensive support and efficiently realise individual requirements thanks to flexible manufacturing processes. You can rely on "Made in Germany" quality for innovative solutions in the production, storage and distribution of hydrogen.
More than 50 years of experience in the development & series production of electromagnets.
CNC, welding, soldering, injection moulding assembly (ESD / clean room) and much more.
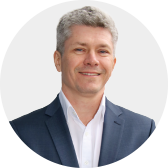

Alexander Grischin
Sales Manager
Proportional solenoid application example
Fuel cell drives
In a fuel cell for a vehicle, a proportional solenoid controls the flow of hydrogen. It precisely regulates the amount of hydrogen flowing into the cell to ensure even and efficient power generation. The solenoid adjusts the gas flow to the current power requirement of the vehicle, enabling optimum utilisation of the fuel cell. This precise control prevents oversupply or undersupply and thus helps to maximise energy efficiency.
Technical requirements
How Magnetbau Schramme solves the technical requirements
Electromagnets in the hydrogen sector must fulfil high technical requirements. They must work reliably in extreme environments with high pressures and temperatures, be resistant to corrosion ("hydrogen embrittlement") and enable precise control.
High energy efficiency is also crucial in order to minimise losses in sensitive applications such as valve controls, compressors or conveyor systems. Their design may even need to fulfil ATEX requirements and other international standards for use in hydrogen systems.
- Proportional solenoid for high-pressure control unit
- Switching solenoid for tank valves or drain valves
- And many more
More information about electromagnets in the hydrogen sector
1. Solenoid types
Valve solenoids, proportional solenoids, linear solenoids and solenoid valves are mainly used in the field of hydrogen technology. They precisely control the hydrogen pressure, the volume flow in supply systems and ensure reliable function at high pressures and temperatures. These solenoids fulfil the strict requirements of modern hydrogen applications, especially in vehicles and systems, and make a decisive contribution to efficiency and safety.
2. Industry-specific technical requirements
Electromagnets in the field of hydrogen technology must fulfil the highest technical requirements. They must work precisely under extreme conditions, such as high pressures (up to 1050 bar), low temperatures (down to -40 °C) and a corrosive medium. The design requires materials with high corrosion resistance, such as stainless steel or special coatings, as well as partially explosion-proof designs in accordance with ATEX directives for safe operation in hydrogen systems. Strict requirements apply for applications in vehicles, such as compliance with functional safety or all requirements from IATF1694, which ensures robust quality and traceability.
Electromagnetic systems are also optimised for energy efficiency in order to minimise losses. Reliability, durability and precision are essential to ensure the safety and efficiency of modern hydrogen technologies.
3. Special features
In hydrogen technology, electromagnets must be particularly pressure-tight and corrosion-resistant in order to withstand the extreme conditions of up to 1050 bar pressure and the chemical aggressiveness of hydrogen. These requirements are significantly more demanding than in many other industries, where such high loads and material requirements occur less frequently.
Electromagnets in the hydrogen sector - Questions & Answers
How does Magnetbau Schramme guarantee the quality and reliability of its electromagnetic drives in the hydrogen sector?
Magnetbau Schramme guarantees the quality and reliability of its electromagnetic drives in the hydrogen sector through specific expertise in product development, the availability and use of specific measurement and validation technology, a high level of vertical integration and strict quality controls. The entire production process - from CNC machining to welding and injection moulding - is carried out to the highest precision standards. In addition, all products are manufactured in accordance with relevant standards such as IATF16949 and ISO 9001. Continuous quality assurance and testing, particularly with regard to pressure resistance, corrosion resistance and functionality under extreme conditions, ensure long-term, reliable performance in hydrogen applications.
Which standards must electromagnets in hydrogen technology fulfil?
Electromagnets in hydrogen technology must fulfil different standards depending on the area of application in order to ensure safety and efficiency. Important standards include the ATEX directives for explosion-protected areas, IATF 16949 for high quality requirements in the automotive sector, ISO 9001 for quality management and ISO 26262 for functional safety. In addition, specific standards such as ISO 15500 for hydrogen vehicle components and UL certifications often apply, which ensure the reliability and safety of the electromagnets.
How does Magnetbau Schramme position itself in the field of fuel cell drives?
Magnetbau Schramme is positioning itself in the field of fuel cell drives as a competent partner for the development and production of electromagnetic components that meet the high requirements of hydrogen applications. Schramme provides reliable solutions, particularly for vehicles such as cars, trucks, buses and rail vehicles equipped with hydrogen fuel cells. The products have to withstand extreme pressure conditions (> 1050 bar) and are manufactured from stainless steel, with precise laser-welded joints ensuring pressure-tightness. Schramme's high level of vertical integration, including CNC machining, welding and quality assurance, ensures customised, high-quality solutions for hydrogen propulsion.
How does a hydrogen combustion engine work and what role do electromagnets play?
A hydrogen combustion engine basically works like a petrol or diesel engine. However, dosing or injecting the hydrogen gas is more complex and complicated. Electromagnets are used in injection systems to control the injection valves. They open and close the valves precisely to inject the hydrogen into the combustion chambers. Electromagnets also play a key role in the hydrogen supply line from the tank to the combustion engine. They control the hydrogen volume flow by precisely opening and closing valves. This is the only way to ensure smooth operation of the engine.
What is the task of a proportional solenoid in a high-pressure control unit for hydrogen drives?
A proportional solenoid in a high-pressure control unit for hydrogen drives controls the volume flow or pressure of hydrogen by precisely regulating valves. It responds proportionally to electrical control signals, allowing the hydrogen flow to be fine-tuned according to the requirements of the system. This enables precise pressure control, prevents overpressurisation and ensures a safe, efficient supply of hydrogen to fuel cells or other components in the powertrain.
How does a fuel cell work in an electric vehicle?
A fuel cell in an electric vehicle consists of an anode, cathode and a cooling heat exchanger. Hydrogen is fed into the anode chamber via a metering unit and a gas jet pump, while air flows into the cathode chamber as oxygen. The reaction between hydrogen and oxygen produces electricity, which drives the electric motor. Unused hydrogen is recirculated back into the anode chamber. Excess energy is stored in an energy storage unit (e.g. battery). The product water is collected in the storage volume.