Rapid development, validation & industrialisation.
Seat valves
Are you looking for a reliable partner for high-quality poppet valves? You've come to the right place at Magnetbau Schramme! As a specialist in the development and production of customised seat valves, we offer innovative and precise solutions that are precisely tailored to your specific requirements.
You can rely on our many years of experience and expertise to make your project a success.
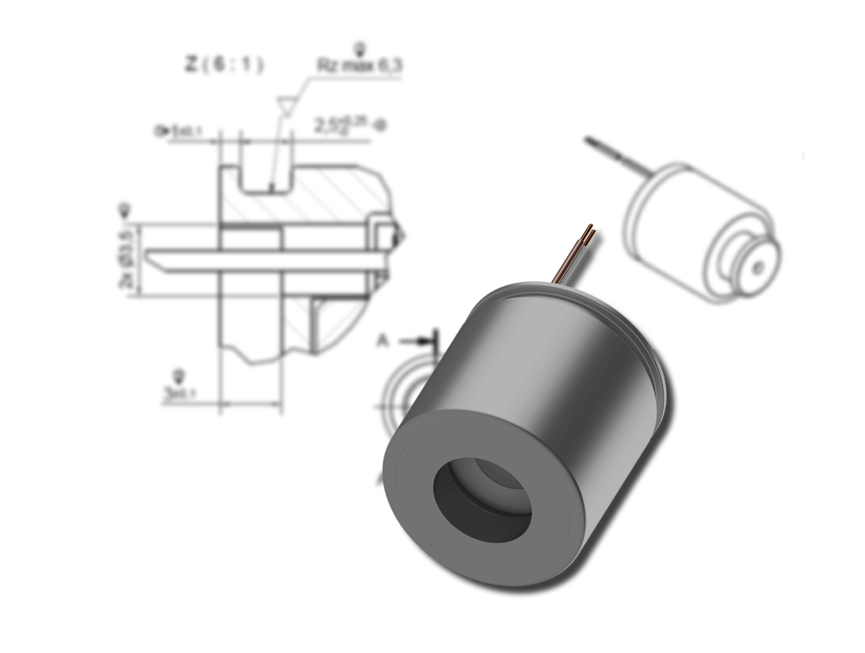
Development and production of poppet valves
Our performance and expertise. Your success.
Magnetbau Schramme is your experienced partner for the development and series production of poppet valves. With our extensive technical expertise and many years of experience, we offer you customised solutions that are precisely tailored to your specific requirements. From concept development to series production, we guide you through the entire process and ensure smooth implementation at every stage of your project.
Contact us today and let our experts advise you individually.
Please note!
Please note that we do not have any standard products. The following seat valves are merely examples of customer projects realised in series.
Technical data - poppet valves
Experience plenty of different possibilities.
A poppet valve is a shut-off valve that regulates the flow of liquids or gases by pressing a valve cone or disc onto a valve seat. When the valve is closed, the disc completely seals the seat. Seat valves are characterised by precise control and high tightness, making them particularly suitable for applications with high pressure or special tightness requirements.
Do you have any questions about our technical data or other details you would like to discuss? Please do not hesitate to contact us.
Construction size | No limitation, up to a max. construction weight of 15kg. |
Nominal voltage range | 6V, 12V, 24V, 36V and others |
Magnetic stroke | up to 3mm |
Force | up to 100N |
Protection class / protection type | up to IP6K9K |
Electrical connection | Free stranded wires, surface-mounted connectors, integrated (moulded) connectors, etc. |
Special features | Pressure-resistant, Normally Closed and Normally Open, low leakage rate, maximum corrosion resistance |
Development & series production
Magnetbau Schramme is your specialist in the development and production of seat valves and further solenoids.
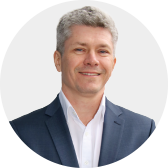

Alexander Grischin
Sales Manager
- Requirements analysis
- Feasibility assessment
- Product concept
- Calculation, simulation
- Individual parts, assemblies
- Final assembly
- Functional test
- Proof of technical suitability
- Tools, equipment
- Quality, logistics
- Procurement, production
- Assembly, EOL testing
More information about poppet valves
How a poppet valve works
A poppet valve is a special shut-off valve that controls liquids or gases by selectively opening and closing a valve seat.
- At its core, the valve consists of a cone or valve disc that is pressed into the valve seat to block the flow or lifted to allow the flow. The valve seat forms a precise fit that ensures a secure seal, even under high pressure.
- The seat valve is actuated by electromagnetic actuators. The precise closing of the valve disc on the seat ensures a leak-free seal, which is particularly advantageous in applications with high sealing requirements such as in the chemical and food industries or in liquid gas systems.
- Seat valves offer high switching cycle stability and a long service life, as they are robustly built and work reliably even with frequent opening and closing operations. They are suitable for both control and shut-off functions.
Designs and types of seat valves
- Square seat valves: These seat valves have a rectangular body profile. Thanks to their compact design, they are particularly suitable for applications with limited installation space. They can be easily integrated into different systems and offer reliable sealing and control performance for the precise flow of media, depending on the design and actuation mechanism.
- Round seat valves: These valves have a cylindrical body, which often makes them more cost-effective as they can be manufactured from simpler components.
Performance parameters seat valves
- Tightness: Tightness describes the ability of the poppet valve to prevent leakage when it is closed. A high level of tightness is crucial to reliably stop the flow of liquids or gases and thus ensure the efficiency and safety of the system.
- Flow rate: The flow rate in litres per minute (L/min) is the volume of medium that can flow through the valve per unit of time. It is determined by the design and valve diameter and is important for the design and dimensioning of the seat valve.
- Pressure loss: The pressure loss (in bar) is the pressure drop that occurs when the medium flows through the valve. A low pressure loss is desirable as it minimises energy consumption and increases the efficiency of the entire system.
- Temperature range: The temperature range in degrees Celsius (°C) indicates the temperatures at which the poppet valve functions reliably. Poppet valves must be suitable for the respective application to protect materials and seals from thermal damage and ensure long-term performance.
- Actuating force: The actuating force in Newtons (N) is the force required to open or close the valve. It depends on the valve design and the actuating mechanism and is crucial for the selection of suitable actuator systems.
- Materials: The materials of the seat valve influence its resistance to corrosive media and mechanical stress. High-quality materials such as stainless steel or special plastics are important for the durability and reliability of the valve in demanding applications.
Structure of the poppet valve
- Body: The body of the seat valve forms the outer frame and is usually made of robust materials such as stainless steel or brass. It contains the other components and provides the structure and stability of the valve.
- Valve disc (or valve cone): The valve disc is the moving component that presses directly on the valve seat to stop or allow flow. Its shape and size are decisive for the tightness and flow of the valve.
- Valve seat: The valve seat is the solid or elastically deforming surface on which the valve disc presses when the valve is closed. It is precisely manufactured to ensure optimum tightness and prevent leakage.
- Seals: Seals made from materials such as elastomers or PTFE are fitted between the moving and fixed parts to prevent leaks and ensure the valve is leak-proof. They are very important for the longevity and functionality of the valve.
Applications Seat valve
- Food and beverage industry: In the food and beverage industry, poppet valves ensure hygienic processing and transport of liquids. They are often made of stainless steel and comply with strict hygiene regulations.
- Automotive industry: Seat valves are also used in various automotive systems, such as fuel systems or cooling systems, to precisely control the flow of fluids and improve the efficiency of the vehicle.
- Chemical industry: Seat valves are used in the chemical industry to safely control aggressive media and chemicals. They ensure precise flow control and prevent leaks that could lead to dangerous situations.
- Water and wastewater technology: Seat valves are used in water treatment plants and wastewater systems to regulate and control the flow of water. They contribute to the safe handling of drinking water and the treatment of waste water.
- Oil and gas industry: Seat valves are used in the oil and gas industry to control the flow of crude oil, gas and other media. They are designed for use at high pressures and temperatures and ensure safe handling.
- Power plant and energy systems: Poppet valves are used in power plants to control the flow of steam, water and other media. They are crucial for the efficiency and safety of power generation plants.
Control and regulation poppet valve
- Actuation: Seat valves from Magnetbau Schramme are actuated electromagnetically. Such automatic actuators control the valve opening quickly and precisely, which improves response time and efficiency.
- Control: Poppet valves control the flow by adjusting the opening based on parameters such as pressure and temperature. Automation systems with sensors and digital controls enable precise control algorithms to ensure stable conditions and avoid pressure or temperature fluctuations.
- Tightness and safety: Tightness is crucial for preventing leaks and for operational safety. High-quality seals and precise valve seats ensure reliable closing, even at high pressures.
Environmental requirements for poppet valves
- Temperature range: Seat valves usually have to work reliably in a wide temperature range from -40 °C to +150 °C without their performance being impaired. High temperatures can lead to overheating and sealing problems, while very low temperatures can make the material structure brittle and impair the valve's functionality. It is therefore crucial that the materials used and the design of the seat valve are suitable for the specified temperature range.
- Types of protection: Depending on the application environment, seat valves are equipped with different types of protection (e.g. IP protection classes) to protect them from dust, moisture and other environmental influences. These protective measures are crucial to ensure the long-term functionality and reliability of the valve under demanding operating conditions.
Seat valves - Questions & Answers
What are the functions of poppet valves used as directional control valves in hydraulics?
Directional control valves in hydraulics control the path of the hydraulic oil and therefore the flow and direction of movement in a hydraulic system. They enable the oil flow to be switched on and off as well as switching between different lines or consumers, such as cylinders or motors. In this way, they regulate the direction of movement and speed of hydraulic drives.
What is the advantage of an angled seat valve over a straight seat valve?
An angled seat valve offers lower flow resistance compared to a straight seat valve due to the angled arrangement of the valve seat, which improves the flow rate. This design enables a higher flow rate with a more compact design. In addition, the angled seat ensures a longer service life for the seals, as wear is reduced due to the smoother closing movement.
What is the difference between a poppet valve and a piston valve (cartridge valve)?
A poppet valve closes the flow through a tightly closing, movable valve plate that is pressed onto a seat, enabling particularly tight and leak-free closures. A gate valve, on the other hand, regulates the flow by moving a gate into an orifice, which provides a less tight seal but is often preferred for higher flow rates. Poppet valves are typically more reliable at high pressures, while piston valves (cartridge valves) are used for larger flow cross-sections and easier maintenance.
What does a 5/2-way valve do?
A 5/2-way valve controls the flow of air or liquid in pneumatic or hydraulic systems. It has five ports and two switching positions to divert the flow between different channels. It is typically used to control double-acting cylinders to allow them to move in both directions.
What is a 4/2-way valve?
A 4/2-way valve has four ports and two switching positions that control the flow of gases or liquids. It is often used to control single-acting or double-acting cylinders by changing the direction of the pressure flow. In one position, it directs the pressure to one port, while in the other position it reverses or vents the pressure flow.