ISO 9001 & IATF 16949 certified as developer & producer of electromagnets.
Machines & systems
Find out how our advanced electromagnet solutions and pioneering technologies are redefining the development of modern machines and systems.
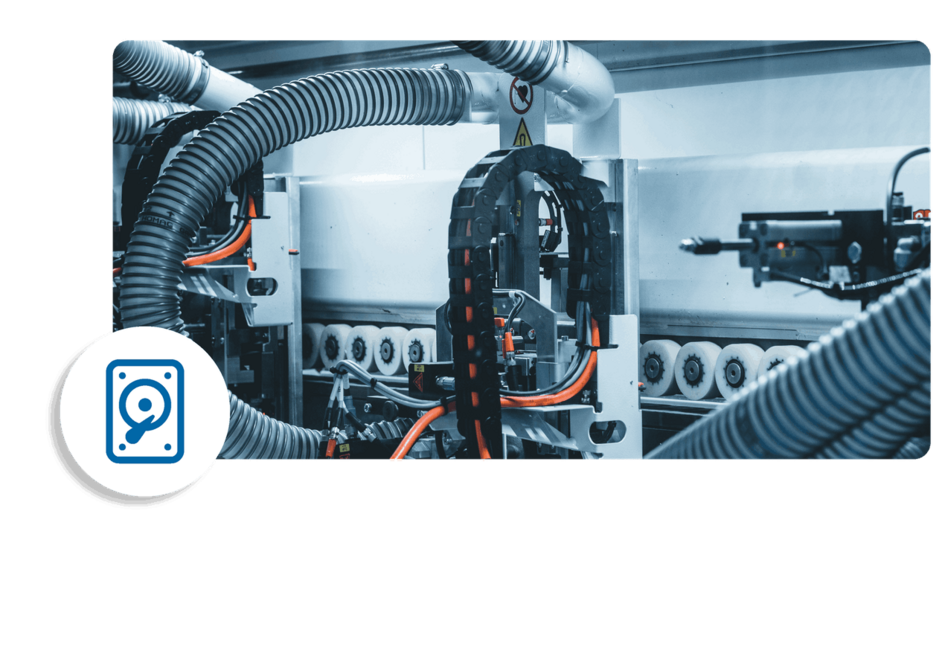
Use of electromagnets
Reliability and speed: electromagnets optimise technology in machines and systems
Electromagnets such as linear solenoids, holding solenoids and valve solenoids play a central role in modern machines and systems. They utilise controlled magnetic force to precisely move, fix or control mechanical components.
Application examples for electromagnets in machines and systems
- Linear solenoid for locking and interlocking handling systems
- Switching solenoid for activating grippers in conveyor technology
- Proportional solenoids for fine adjustment of movements for robot technology
- And many more
Precision and reliability in demanding applications
Linear solenoids enable linear movements, while holding solenoids securely hold components in place. Valve solenoids control the flow of liquids or gases in pneumatic and hydraulic systems. Thanks to their reliability, high switching speed and adaptability, these solenoid types are used in numerous applications such as automation, robotics and process technology. Their targeted selection and integration optimise the functionality, efficiency and safety of technical systems.
Your advantages with Schramme
Development and production of electromagnets for machines & systems
Magnetbau Schramme is your competent partner for the development and series production of high-quality electromagnets for machines and systems. With decades of experience, we offer customised solutions that meet the highest demands for precision, reliability and technical standards.
From the initial idea to series production, we provide you with comprehensive support and efficiently realise individual requirements through flexible production processes. You can rely on proven "Made in Germany" quality for your innovative applications in mechanical and plant engineering, whether in automation, process technology or other future-oriented areas.
More than 50 years of experience in the development & series production of electromagnets.
CNC, welding, soldering, injection moulding assembly (ESD / clean room) and much more.
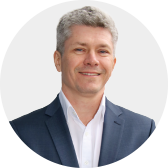

Alexander Grischin
Sales Manager
Application example: linear solenoid
Interlocking handling systems for injection moulding machines
A linear solenoid in a handling system of an injection moulding machine is used for the precise locking and interlocking of moving parts. Thanks to its electromagnetically generated stroke movement, it fixes components securely in a defined position or releases them in a targeted manner. This ensures reliable positioning and stability of the system during operation, thereby increasing process accuracy and safety.
Technical requirements
How Magnetbau Schramme solves the technical requirements
The technical requirements for electromagnets in mechanical and plant engineering include precision, reliability and efficiency. This includes service life, heat resistance, energy consumption and tolerances. Safety guidelines and standards as well as quality requirements, usually in accordance with ISO9001, are standard and help to ensure that, for example, the traceability of products is guaranteed and documented test processes and risk assessments are available.
The requirements for proportional solenoids are defined, mostly linear force-displacement characteristics, while switching solenoids often focus on fast switching times. Most solenoid systems must fulfil EMC guidelines and enable mechanical integration into compact machine layouts.
- Linear solenoid for locking and interlocking handling systems
- Switching solenoid for activating grippers in conveyor technology
- Proportional solenoids for fine adjustment of movements for robot technology
- And many more
More information about electromagnets for machines and systems
1. Solenoid types
The following electromagnet types are used in machines and systems: switching solenoids, proportional solenoids, linear solenoids and double-stroke solenoids for motion control, holding solenoids for fixing, solenoid valves (e.g. seat and slide valves) for fluid control, electromagnetic clutches and brakes for drive systems as well as magnetic bearings for frictionless, contactless bearings.
2 Industry-specific technical requirements
Electromagnetic drives in machines and systems must offer maximum precision, reliability and energy efficiency. Industry-specific requirements include fast switching and response times for dynamic processes, high holding forces for fixings and linear control characteristics for proportional solenoids for precise control tasks. The design must be robust, compact and durable in order to withstand harsh industrial conditions. Heat resistance and mechanical stability are crucial, especially in high-performance and continuous operation. As part of ISO 9001 and other quality requirements, traceability of products and components, documented quality checks and clear process controls must be guaranteed.
Integration into automated systems and the reduction of energy consumption are also playing an increasingly important role.
3. Special features
The mechanical and plant engineering sector requires extremely robust, durable and precise electromagnetic drives that can withstand harsh environmental conditions such as high temperatures, vibrations and dirt. In addition, short response times and seamless integration into complex, often customised automation systems are essential.
Electromagnets for machines & systems - Questions & answers
What are the legal requirements and standards for electromagnetic drives in machines and systems?
Many legal requirements and standards apply to electromagnetic drives in machines and systems. IEC/EN 60947-5-1, for example, regulates the safety of electrical control devices, including electromagnetic switching devices. ISO13849 and ISO10218 define safety requirements for machine controls and robots. Drives must also fulfil the RoHS directive for environmentally friendly materials and often comply with EMC directives on electromagnetic compatibility. In addition, ISO9001 requires a quality management system that ensures continuous improvement, process controls and product traceability.
What role do electromagnetic drives play in robotics?
Electromagnetic drives are indispensable for the precise control of robot arms and grippers. Proportional solenoids enable finely dosed force control, allowing robots to move loads smoothly and safely. Holding magnets securely hold components in place during processing. Their fast response time and compactness make them ideal for dynamic movements, for example in collaborative robots or in logistics automation, where they make work processes flexible and efficient.
How robust are electromagnetic drives?
Electromagnetic drives from Magnetbau Schramme are designed for use in extreme environments. They can withstand high temperatures, vibrations and dirt, which makes them ideal for use in production machines, heavy industry or mobile robots. Thanks to their high protection ratings, such as IP65 or higher, they are also protected against moisture or dust and remain precise and durable even under harsh conditions.
Can electromagnetic actuators be used in portable devices?
Yes, the compact design and precise control of electromagnetic actuators make them ideal for wearable applications such as exoskeletons or surgical robots. In these devices, they enable precise movements that can be finely dosed and repeated. Their energy efficiency and low heat generation are essential, as wearable systems rely on lightweight battery operation. They therefore support modern, highly innovative applications in the field of medical and rehabilitation technology.
What safety benefits do electromagnetic brakes offer?
Electromagnetic brakes ensure fast and safe stopping of movements, e.g. in production machines or robots. They grip precisely and prevent uncontrolled movements, which makes a decisive contribution to occupational safety. In robots in particular, they prevent damage to people or components in the event of power failures or overloads. Their reliability and adaptability make them indispensable for modern, safety-critical applications.
How do electromagnetic drives contribute to digitalisation?
Electromagnetic drives can be seamlessly integrated into digital control systems. With embedded sensors and intelligent control, they provide real-time data for monitoring and optimisation. In Industry 4.0, they enable adaptive processes, for example by automatically adjusting to production requirements. They also enable remote monitoring, allowing system operators to recognise problems at an early stage and plan maintenance more efficiently, which reduces downtime.